Simulator flying mimics the real thing. Display visuals show realism. There are sound effects for engine and other aircraft equipment noises. The aircraft cockpit flight controls, switches, indicators, and instruments are identical to those of the actual cockpit. Since the machine is perched upon electric actuator struts that can raise, lower and tilt the box in all axis “G” forces are mimicked. Vibrations can be discerned when taxing across tarmac expansion joints or the thump thump thump encountering flush mounted runway centerline lights during takeoff roll.
The simulator doesn’t actually have landing gear or wheels but amusing when you realize that the device has tricked you into believing that it sure seems like it does. The interaction between brain, eye, small of your back, seat of your pants largely takes you in. When applying brake pressure for instance the simulator box dips forward which allows a sensation of deceleration. But the inner ear is not perfectly fooled. Steering a 90 degree turn on an airport taxiway can be nauseating. It is best not to stare too hard at the video presentation in the cockpit window. (When it’s my turn in the co-pilot seat, I don’t even look; keeping eyes in.)
Despite the nitpicks, the experience is real enough and deemed by the regulators to suffice for full blown training and qualification testing. A new pilot will complete the course regimen solely in this device and obtain his Aircraft Type Rating without having boarded the actual airplane before. His first flight (non-simulated) may even have [oblivious] passengers onboard!
A crucial advantage of simulator flying is that many “what if” events can be experienced without putting man or machine at physical risk. Challenging scenarios can be allowed to play out to successful outcome. Before the adoption of advanced full motion simulation, emergency drills where “simulated” in an airborne aircraft. An instructor pilot would surreptitiously reach for an engine power lever and snap it closed to observe a pilots response procedure. This usually worked out fine, as long as everyone stuck to a certain script. Multi-engine aircraft can fly just fine with an inoperative engine. On the other hand; what could possibly go wrong there?
V1 Cut
This is the demonstration of pilot reaction and the control that is necessary because even though, an aircraft is designed to climb engine out it can go badly if not performed precisely. With a failed engine the thrust centerline is now asymmetric. The aircraft wants to yaw and turn in the direction of the dead engine. There are usually terrain or air traffic control considerations so there may be undesired consequences should the aircraft drift off course suddenly or otherwise. The episode is almost always practiced at V1 (decision speed — the point where there is not enough runway remaining to abort the takeoff and at which you are now committed to take it into the air ) It is a velocity calculated beforehand and a commitment rigidly adhered to. This point is the most challenging moment for an engine “Cut” and the engine can lose thrust gradually (called a roll-back) or altogether as in catastrophic failure (associated with a loud bang)
The pilot’s (PF — pilot flying) first task is to counter immediately and correct with opposite rudder. The direction of the yaw may come into eye view as the nose of the plane tends to depart the runway centerline and aims itself for the green grass off pavement. The rudder pedal is used to restore directional control. The rudder surface has low effectiveness at this speed so a massive deflection is necessary; meaning with exertion you push your foot all the way to the floor holding it there. Your scan moves from outside to instruments on the inside because, recall we also had to get airborne and we have simultaneously rotated the aircraft into a pitch up movement to do so. The pilot’s attention is divided across directional control, pitch attitude, and [V2] airspeed. The tolerances are narrow. With disciplined scanning, proper assessment and deft control placement a desired result happens — laterally and vertically. With a positive rate of climb the pilot brings in the second pilot as a resource. This pilot {PM — pilot monitoring) verifies and calls out “positive rate”. The PF calls “gear up”. The entire script is well choreographed and each pilot knows exactly what each is expected to say and do and when. We call these [memorized] actors’ lines.
We are not out of the woods yet. As the aircraft accelerates the rudder gains effectiveness and therefore less deflection is required. The PF constantly adjusts his leg pressure thus maintaining coordinated flight and managing desired heading. A previously calculated [takeoff] flap retraction altitude is reached and the PM announces “FRA”. The PM accelerates the aircraft to the faster and appropriate [Vfs] climb speed and commands “flaps zero”. The climb continues to the briefed safe altitude at which time emergency checklists are performed, ATC advised and their resources utilized. A plan of action is decided upon and briefed and so it goes.
This kind of actual event is extremely rare. I’ve only experienced an engine failure once in my flying career (through 4,000′ on climb out) but just the same we prepare for it and the simulator is an ideal stage.
Elec XFR Fail
This is another time critical event. In the rare occurrence of a dual gen fail and in an effort to conserve battery power the automation will reconfigure the system to shed nonessential loads. CAS warning/caution messages post to the PFD but the bigger give away is the dark cockpit with loss of lighting and blank display screens. You’ve lost a host of other systems too –everything on DC BUS 1 and DC BUS 2 (pitch trim norm and pitch trim bkp — oh dear) In this electric transfer fail scenario, the described reversion didn’t automatically happen and, time critical, because battery life will be severely impaired.
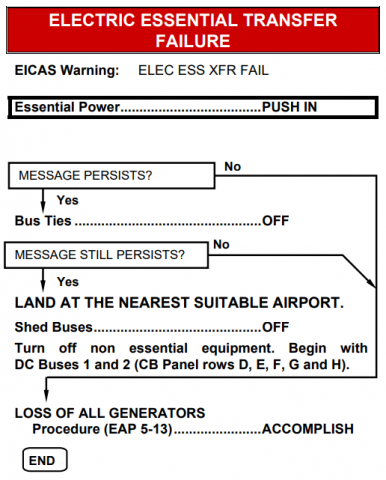
Time is of the essence. The Quick Reference Handbook (QRH) directs the PM to press the ELEC EMER Button, the manual method which overrides the EPGDS, connecting BATT 1 and BATT 2 directly to the EMERGENCY BUS. If this was successful you’ve bought some time but you’re still dealing with the lesser of the two evils, the ELEC EMERGENCY [CAS]. The PF has got his hands full trying to maintain pitch control. (The simulator instructor gave us this one right after takeoff so the aircraft/sim was nose high on trim. I could only arrest the climb by wedging by knee into the control yoke providing thigh muscle assist.) The PM is still in the QRH with the next CAS as the aircraft/sim cabin pressure is escaping and will soon manifest another set of issues. In hindsight, because of our low altitude, we could have cut to the chase and zoomed to the final checklist line; giving my arms a break:
Generators 1 and 2 .................. OFF, THEN AUTO
This ultimately reestablished things as one of the generators came back online. I had my instrumentation and pitch trim and systems restored.
Good thing to demonstrate and to see — in a simulator that is.
A-I WINGSTB LEAK
This cautionary CAS alert directs the PM to a checklist flow chart to try and isolate the source of a bleed leak. Bleed is high pressure air that is used for cabin pressurization, ECS, and airframe anti-icing. Air gains heat when compressed so hot bleed impinging upon unprotected structure is bad. Through the process of elimination we were able to switch to off the errant bleed. The QRH gave further direction to leave icing conditions whilst recommending necessary precaution for degraded performance for the approach and landing phase with Flaps limited to Flaps 1.
We executed and uneventful touchdown at the Pittsburgh Intl Airport — simulated naturally.
A-I E1 (2) FAIL
We saw this one; the anti-ice engine 2 fail CAS. Noticeable vibration developed (yes, the sim does) but before we could action the NAP1-16 reference procedure the engine spooled down. This led to an engine inop approach and landing exercise.
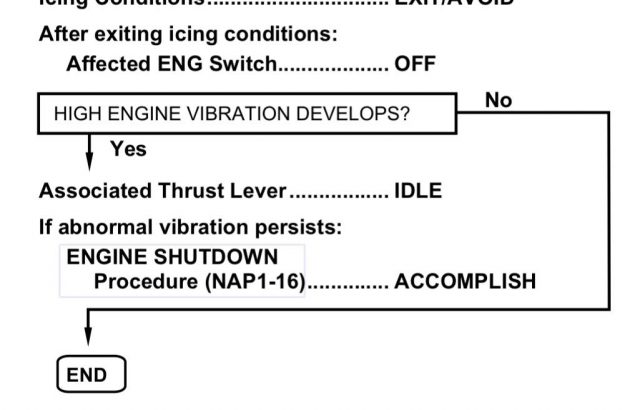
Rules of the Game
Each scenario practiced results in a successful outcome. That of course is desired as it gives good experience should such an event play out in actuality. Positive training.
The sim instructor is not allowed to over-task the pilot with multiple scenarios, at least not at the same time. A windshear situation or terrain escape maneuver would never be compounded with a loss of cabin pressure as an example. Problems can and do coexist of course. e.g. engine fire > single engine approach to landing So, each problem is carefully worked through logical step by step to conclusion before another one begins.
The order of problem solving is by priority importance. For instance, you might think that the first concern during an engine fire is to fight the fire but that is not the case. Number one is to fly the airplane. Maintain control.
After reaching a [briefed] safe altitude we may be required to perform an emergency checklist from memory or Quick Reference Checklist (QRC), or QRH in that order, then we deal with the more “mundane”. Memory items cover immediate action items:
- Cabin smoke
- Cabin depressurization
- Dual engine failure
- Inadvertent pusher activation
- Evacuation
- Start Malfunction
After a 2 hour drill we generally take a 10 minute pause and then swap seats to finish with another 2 hours of excitement. Thus ends the sim session. There are 236 unique CAS messages that lurk so there will always be stuff to see for the next time.
Now you’re prepared!