The RV-14 rudder requires a fair amount of precision. Its surface controls aircraft yaw and as an aerodynamic foil it must also be slippery (low drag) as it moves through the air upwards of 200 MPH. The feature to get right, is the trailing edge (TE) which slims to a pointed ending. It must be straight and true without twist.
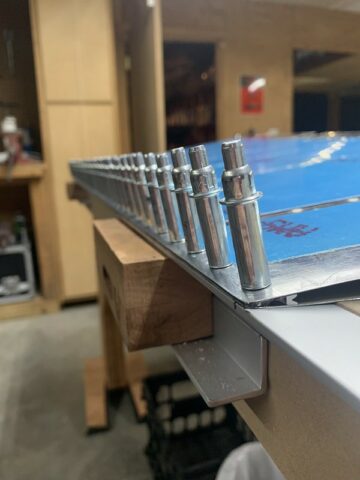
Observe the underlying aluminum angle bar fixed to the workbench in the photo. While the bench itself is quite flat, the aluminum straight edge clamped to the TE will minimize any pucker or wave tendency in the skin. The skin is quite thin (0.016″) and needs the support. A preformed wedge is sandwiched between the right and left skins as you can just make out inside the TE of the rudder (lying on side).
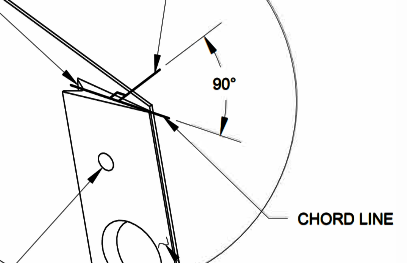
The TE wedge is machined so that its rivet thru holes are angled properly. They are matched drilled 90 degrees with reference to the chord of the wedge. The holes are also machine counter sunk so that the dimpled skin will lie within for an interference fit that also allows the skin to lie flush upon them.
An adhesive seal provides a bond between skin and wedge. Once the sealant cures the cleco clamps can be removed and the sandwich permanently fixed in place by riveting. With this effort the structure will be robust and provide good handling characteristic without adverse yaw or drag whilst cleaving the sky. Straight and true.