This photograph is hand dated 1910. The Randrup family lived in Copenhagen (København) Denmark The letter K on the registration plate so designates. The owners hand draped over the front seat armrest and his shoe on the running board seem to be rather crudely inked out. (early days for photoshop)
The carbide headlamps used acetylene gas but the side marker lamps were oil burning and that may explain why the lense on the passenger side is blackened. It would have been used, as required, for street side parking during the night.
There’s a folding top but it’s a fair weather open car without windshield or side windows. I would say very low mileage based upon the state of clean and shine. See the messy bits on the pristine roadway substrate inside of the front year tire. I hope that this automobile wasn’t blamed. Good reason to check your shoes before coming indoors!
The 1910 Randrup family photo op featuring the brass era touring car above has been identified. It was a difficult task because I only had the first 3 design letters visible on the radiator: “Ber” and come to think of it; that longhand script style was pixelated and no doubt in a foreign language to boot.
Typing just three letters into a Google Search did not result in a handy autofill suggestion! I did however manage to find a comprehensive list of makes whose name began with the letter B. Matching up the next two letters narrowed that list considerably and voila. After selecting a few of these near matches, comparing images of early cars, fender and radiator shapes I found a match. The dead ringer confirmation is the unique “B” signature script of the name on the radiator which was clear in other comparison photo records.
It’s a French made Berliet motorcar and as a company went on to a long history but one not well known in the USA — except for one obscurity. The Berliet design and manufacturing rights were licensed to the American Locomotive Company of New York. They attempted to capitalize on an American perceived exotic european excellence theme but note that the eye catching brass Berliet logotype on the radiator was struck.
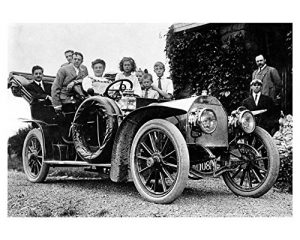