Inner skeletal structure
Once encapsulated by (0.032) 2024-T3 sheet aluminum the vertical stabilizer will be quite robust. The spars and interconnecting ribs enhance rigidity while retaining light weight. The outer skin will tie it all together. The spars are of the same material spec as the skin. To add backbone i.e. rigidity extra material is strategically employed. This doubler material is of greater thickness (0.125″). You will observe the large diameter holes in the doubler; they are for weight reduction.
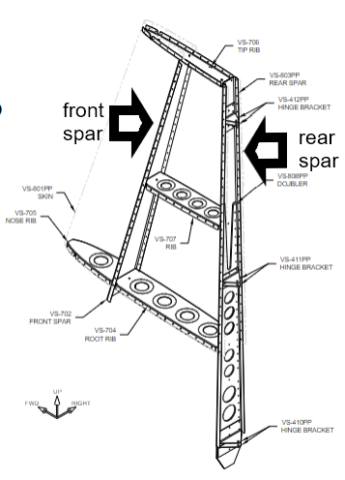
Pre-Punched – In the kit manufacturing process the vendor enhances the product by machine piercing the rivet holes. The machine has a much more precise tolerance than any amateur in their positioning. In this application they are slightly undersize at 1/8″ (0.125)
Doubler – A small piece of plate attached to a larger area of plate that requires strengthening in that location
As described in the video clip the manufactured holes must be enlarged from 0.125 to final size 0.1285 in a process called finish drilling. I use a #30 reamer for this purpose.
A reamer is a rotary cutting tool that is used to enlarge and finish holes that have been drilled, bored, or cored. Reamers are designed to center themselves in an existing hole, which results in a rounder hole and with fewer burrs.
Thanks to the precision of the pre-punched holes everything generally will line up for excellent fitment. When alignment is crucial a process called match drilling is employed. A piece that already has pre-punched hole(s) is used to center an underlying piece which does not. The former acts as a guide for the drill bit once the two are mated.